Silicon Carbide Ceramic Materials
Due to their excellent wear resistance, thermal conductivity, oxidation resistance, and outstanding high-temperature mechanical properties, silicon carbide (SiC) ceramics are widely used in precision bearings, seals, gas turbine rotors, optical components, high-temperature nozzles, heat exchanger parts, and nuclear reactor materials. However, the strong covalent bonding and low diffusion coefficient of SiC pose significant challenges in achieving sintering densification during fabrication. Thus, sintering processes are critical for producing high-performance SiC ceramics.
Current methods for preparing dense SiC ceramics include reaction bonding (common), pressureless/atmospheric sintering (common), recrystallization sintering, hot pressing, and hot isostatic pressing. The properties of SiC ceramics vary depending on the manufacturing process. So, what do abbreviations like SSiC, SiSiC, RBSiC, and RSiC represent?
Reaction Bonded Silicon Carbide (RBSiC/SiSiC)
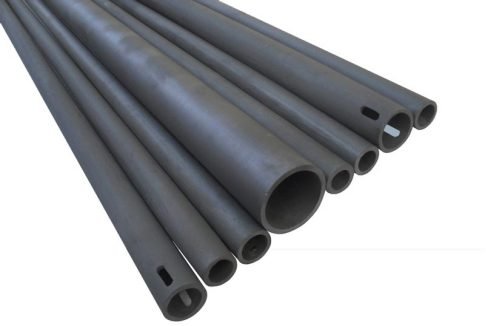
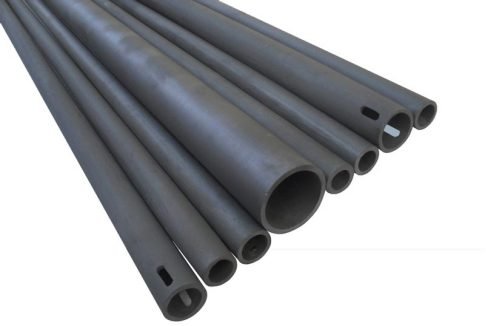
Process Overview
A graded mixture of SiC powder (1–10 μm) and carbon is shaped into a green body. At high temperatures, silicon infiltration occurs: silicon reacts with carbon to form additional SiC, bonding with the original SiC matrix. Two silicon infiltration methods exist:
- Liquid-phase infiltration: At 1,450–1,470°C (melting point of silicon), liquid silicon enters pores via capillary action and reacts with carbon.
- Vapor-phase infiltration: Above silicon’s melting point, silicon vapor infiltrates the green body.
Process Flow:
SiC powder + C powder + binder → shaping → drying → binder removal under protective atmosphere → silicon infiltration → post-processing.
Key Notes
- RBSiC contains 8–15% free silicon, making it a Si/SiC composite rather than pure SiC.
- Free silicon limits operating temperatures to below 1,400°C; strength degrades sharply above this due to silicon melting.
- Vapor-phase infiltration reduces free silicon content (<10%), improving performance.
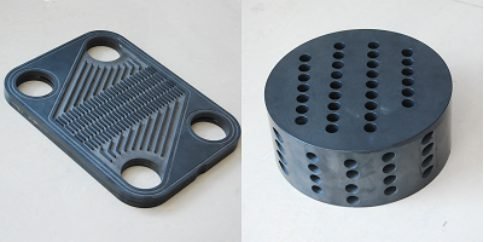
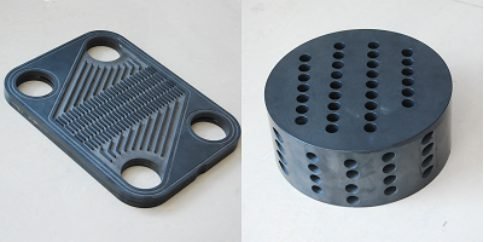
Characteristics and Applications
- Advantages: Low sintering temperature, cost-effective, near-net-shape forming with <3% shrinkage, ideal for large/complex components (e.g., kiln furniture, crucibles, heat exchangers).
- Applications: High-purity RBSiC parts (e.g., semiconductor wafer handling fixtures) replace quartz in electronics. Notable producers include UK’s Refel and Japan’s Asahi Glass.
- Limitations: Free silicon reduces wear resistance and chemical stability (vulnerable to alkalis/HF acid).
Classic Application: Spiral nozzles for gas scrubbing, cooling, and fire suppression.
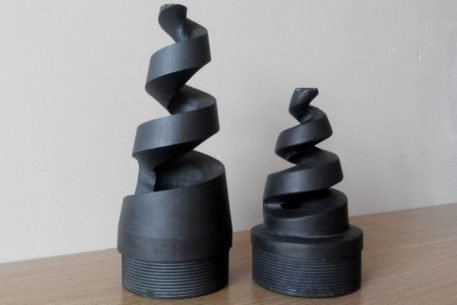
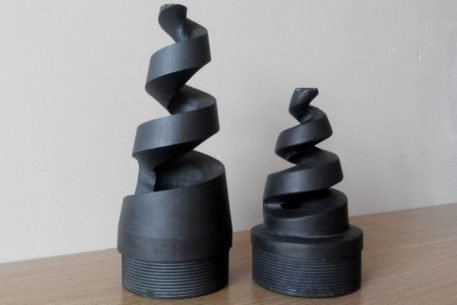
(General applications of spiral nozzles: exhaust gas scrubbing; gas cooling; scrubbing and rinsing processes; fire protection)
Pressureless/Atmospheric Sintered SiC (PSSiC)
Process Overview
Sintering occurs at 2,000–2,150°C under inert gas without external pressure. Additives (e.g., boron, carbon, Y₂O₃-Al₂O₃) promote densification. Two subtypes exist:
- Solid-State Sintered SiC (SSiC):
- Invented by Prochazka (1974) using β-SiC with B/C additives.
- Clean grain boundaries, high-temperature stability (up to 1,600°C), but coarse grains and low fracture toughness.
- Liquid-Phase Sintered SiC (LSiC):
- Uses Y₂O₃-Al₂O₃ additives for lower sintering temperatures.
- Fine grains, improved toughness via intergranular fracture.
Applications
Wear/corrosion-resistant seals, bearings, and structural components.
Recrystallized Silicon Carbide (RSiC)


Process Overview
High-purity SiC powders (coarse + fine grains) are sintered at 2,200–2,450°C via evaporation-condensation without additives. Non-densifying mechanism retains 10–20% porosity.
Characteristics and Applications
- Advantages: Porous structure (interconnected pores), ultra-high purity (>99% SiC), excellent thermal shock/chemical resistance.
- Applications: High-temperature kiln furniture, solar thermal converters, diesel particulate filters, and metallurgical components.
Hot-pressed Silicon Carbide (HPSiC)
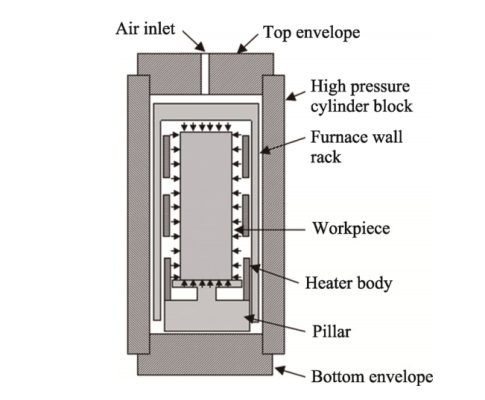
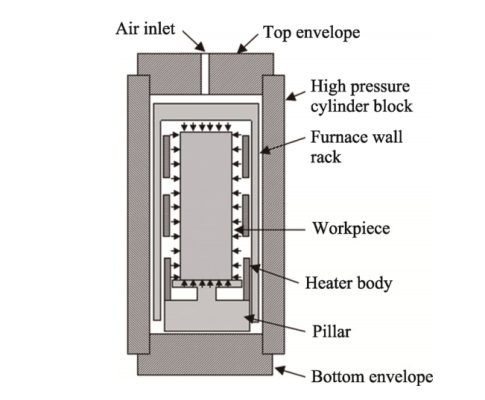
Process Overview
Hot isostatic pressure sintering (HIP) is to make the material (powder, billet or sintered body) in the heating process undergoes various balanced pressure, with the inert gas argon or nitrogen as the pressure transfer medium, with the help of high temperature and high pressure to promote the joint action of densification of the process.
HIP process can be divided into two categories:
1) ceramic powders encapsulated directly after the HIP sintering, i.e., the package set of the HIP process;
2) by the raw material through the molding (a variety of ceramics) Molding process can be), pre-sintering to achieve a certain density, the material is no open pore state, and then by the HIP high temperature and high pressure post-treatment.
Characteristics
- High density, fine grains, superior mechanical properties.
- Limitations: High cost, complex tooling, limited component complexity.
Spark plasma sintering silicon carbide (SPSSiC)


Fast and efficient sintering of materials at low temperatures can be achieved using discharge plasma sintering (SPS).
Firstly, the raw material is placed in a graphite mold (although discharge plasma sintering is similar to hot pressing, it does not use indirect heating by a heat generator, but the current heats the mold and the powder), and then the temperature is rapidly increased and the billet is subjected to pressure and DC pulsed current, and the sintering is completed in a short time (when the current is very high, it generates Joule heat and plasma in the sample, and the rapid densification is achieved within 10 min). (when the current is high, Joule heat and plasma are generated in the sample, and rapid densification is achieved within 10 min, with a relative density of 98-99.5%).
Compared with conventional sintering techniques for the preparation of high-density silicon carbide ceramics, discharge plasma sintering has a faster heating rate, a lower sintering temperature, and a shorter sintering time. At the same time, due to the very short sintering time of discharge plasma sintering, the grain growth of the ceramic material is limited so that fine and uniform grains can be maintained. Similar to hot pressing and hot isostatic pressing, it can be done in less large sizes.
Conclusion
Silicon carbide ceramics demonstrate remarkable versatility across industries, with manufacturing processes dictating their final properties and applications. Reaction bonding (RBSiC/SiSiC) prioritizes cost-efficiency and scalability for large, intricate components, while pressureless sintering (SSiC/LSiC) excels in producing high-purity, wear-resistant parts. Recrystallized SiC (RSiC) thrives in extreme thermal and corrosive environments due to its ultra-high purity and porous structure, whereas hot-pressed SiC (HP SiC) offers superior mechanical performance for specialized, simple-shaped components. Emerging techniques like spark plasma sintering further enhance processing speed and precision. Engineers must balance factors such as operating conditions, material purity, geometric complexity, and budget to select the optimal SiC variant, ensuring alignment with specific industrial demands and advancing technological frontiers.