Silisyum Karbür Üretim Süreci
Üretim süreci silisyum karbür birkaç adım içerir, kaliteli ve güvenilir malzemelerin üretimini sağlamak.
İşlenmemiş içerikler
Silisyum karbür üretiminde kullanılan birincil hammaddeler silikon ve karbondur.. Bu malzemeler özenle seçilir ve safsızlıkları ortadan kaldırmak ve istenen bileşimi elde etmek için titiz bir saflaştırma sürecinden geçer..
Toz Hazırlama
Hammadde saflaştırıldıktan sonra, Çeşitli tekniklerle ince tozlara dönüştürülürler. Silikon ve karbon tozları, istenen silikon karbür bileşimini elde etmek için kesin oranlarda karıştırılır. Tozlar daha sonra öğütülür ve düzgün bir parçacık boyutu dağılımı elde etmek için öğütülür, nihai üründe tutarlılığı sağlamak.
Karıştırma ve şekillendirme
Bu aşamada, Silikon karbür tozları, işlenebilirliklerini ve biçimlendirilebilirliğini arttırmak için bağlayıcılar ve katkı maddeleri ile karıştırılır.. Karışım daha sonra presleme gibi farklı teknikler kullanılarak istenen formda şekillendirilir, ekstrüzyon, veya kayma dökümü. Bu adım izin verir üreticiler Çok çeşitli ürünler oluşturmak için, Karmaşık seramik bileşenlerden taşlama uygulamaları için aşındırıcı tanelere kadar.
sinterleme
Sinterleme, şekilli silikon karbürün yüksek sıcaklıklarda ısıtılmasını içeren kritik bir süreçtir., Tipik olarak kontrollü bir atmosferde veya vakum koşullarında. sinterleme sırasında, Tozlar birbirine bağlanır, gelişmiş mekanik özelliklere sahip yoğun ve katı bir malzeme ile sonuçlanır. Son ürünün istenen yoğunluğunu ve yapısal bütünlüğünü elde etmek için sinterleme sıcaklığı ve süresi dikkatle kontrol edilir.
Bitirme ve kalite kontrolü
Sinterlemeden sonra, Silikon karbür ürünleri, belirli gereksinimleri karşılamak için ek işleme ve bitirme adımlarına tabi tutulur. Bu öğütmeyi içerebilir, parlatma, veya istenen yüzey kaplamasını ve boyutsal doğruluğunu elde etmek için kaplama. Kalite kontrol önlemleri, denetimler gibi, test, ve analiz, Silikon karbür ürünlerinin gerekli standartları ve özellikleri karşılamasını sağlamak için üretim süreci boyunca uygulanır..
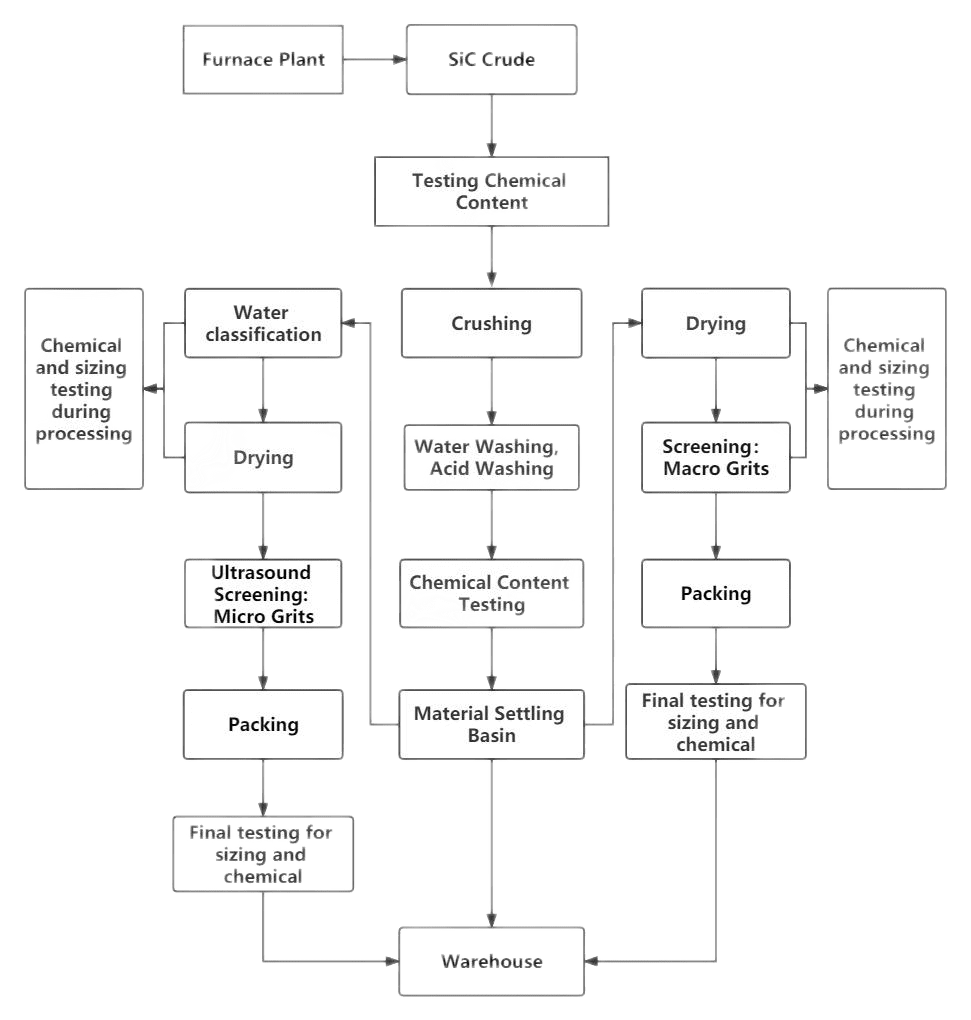
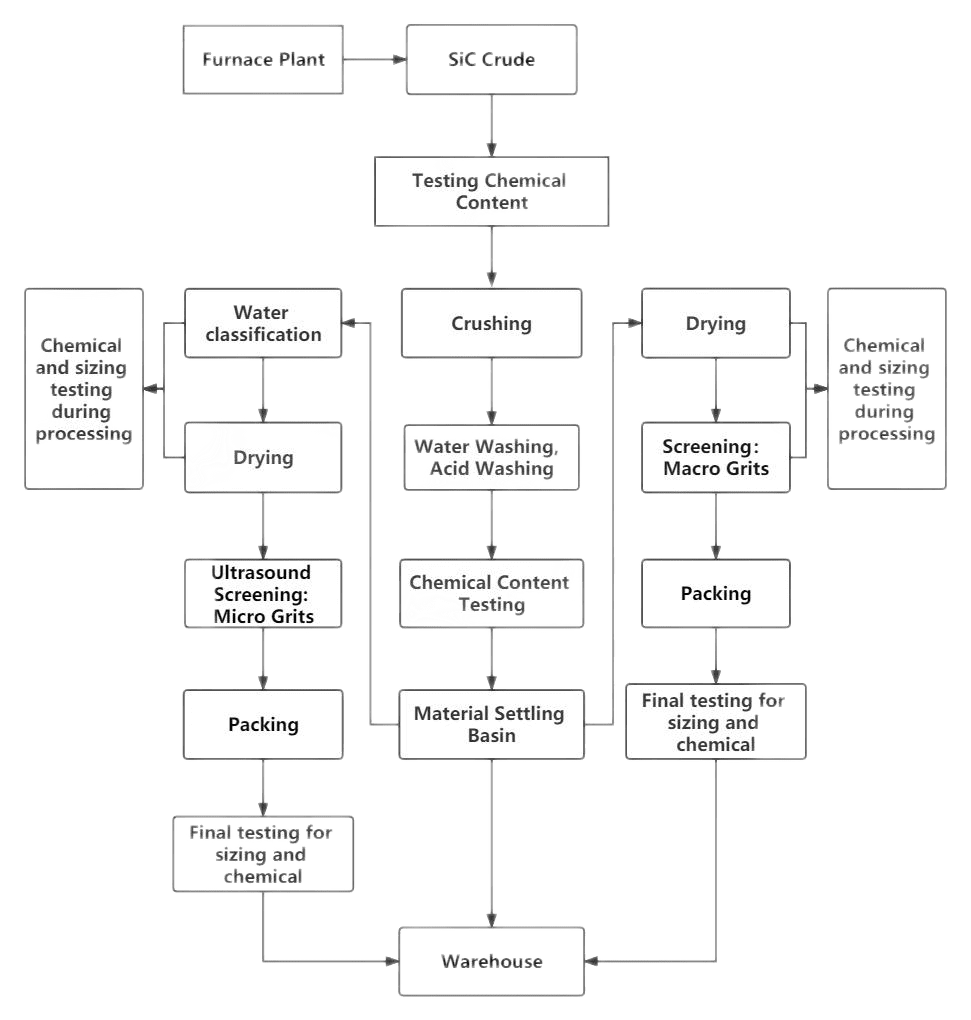
Silisyum Karbür Uygulamaları
Silikon Karbür, olağanüstü özellikleri ve çok yönlülüğü nedeniyle çok çeşitli sektörlerde uygulamalar bulur.. Temel uygulama alanlarından bazıları:
Aşındırıcılar ve öğütme
Silikon Karbür’nin olağanüstü sertliği ve aşınma direnci, aşındırıcı malzemeler için ideal bir seçim haline getiriyor. Üretiminde kullanılır taşlama, kesme aletleri, ve aşındırıcı kağıtlar, Çeşitli işleme ve yüzey bitirme işlemlerinde üstün performans ve genişletilmiş takım ömrü sağlamak.
Seramik ve refrakter
Silikon Karbür’nin Yüksek Gücü, Mükemmel termal şok direnci, ve kimyasal saldırıya karşı direnç, onu üretiminde değerli bir malzeme haline getiriyor seramik ve refrakter ürünleri. Fırın mobilyalarında kullanılır, potalar, ve yüksek sıcaklık bileşenleri, Aşırı ısı ve aşındırıcı ortamlarda güvenilir performansın sağlanması.
Elektronik ve yarı iletkenler
Silikon karbür, elektronik ve yarı iletkenler alanında önemli ilgi görmüştür.. Eşsiz elektriksel özellikleri, yüksek arıza voltajı gibi, yüksek ısı iletkenliği, ve geniş bant aralığı, Güç elektronik cihazları için uygun hale getirin, LED aydınlatma, ve yüksek sıcaklık elektroniği.
Otomotiv ve ulaşım
Otomotiv endüstrisi, çeşitli uygulamalar için giderek daha fazla silikon karbür benimsiyor. Fren diskleri gibi bileşenlerin üretiminde kullanılır, çukur, ve motor parçaları, Üstün performans sunmak, ağırlık azaltma, ve geliştirilmiş yakıt verimliliği. Silikon Karbür Tabanlı Güç Elektroniği de elektrikli araç şarj sistemlerinde devrim yaratıyor, Daha hızlı şarj ve artan güç yoğunluğunu etkinleştirme.
Silikon karbürün avantajları ve dezavantajları
Avantajlar
- Olağanüstü sertlik ve aşınma direnci
- Yüksek termal iletkenlik ve ısı dağılımı
- Düşük termal genişleme ve boyutsal stabilite
- Mükemmel kimyasal direnç
- Geniş bant aralığı ve yüksek sıcaklıkta çalışma özellikleri
- Güç elektroniği için gelişmiş elektriksel özellikler
Dezavantajları
- Diğer malzemelere kıyasla nispeten yüksek üretim maliyeti
- Büyük boyutlu bileşenlerin sınırlı kullanılabilirliği
- Silisyum karbürün sertliği ve kırılganlığından kaynaklanan işleme zorlukları